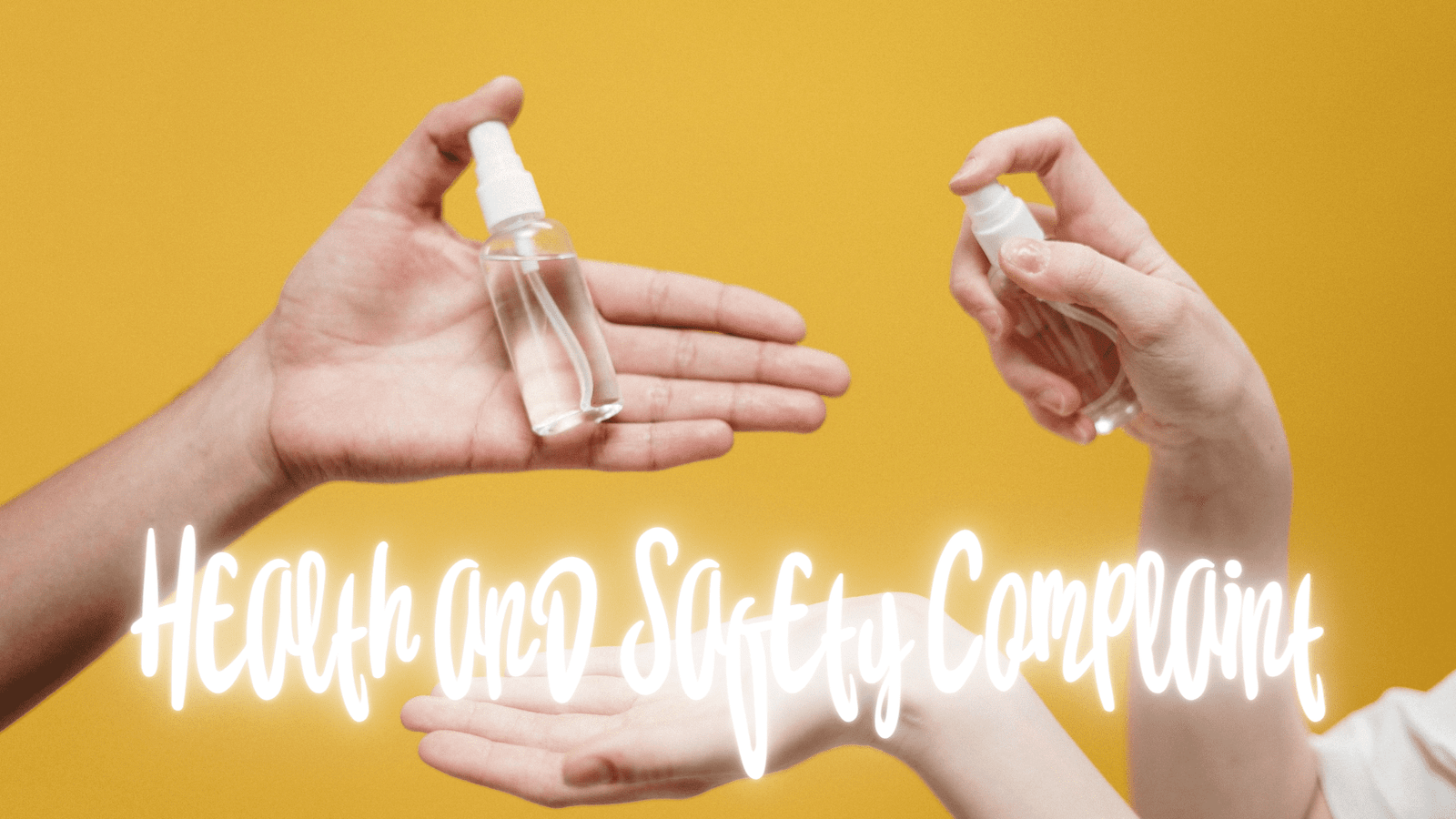
Health and safety complaints are critical to maintaining a safe and secure work environment. They not only highlight potential hazards but also help organizations address issues before they escalate. In India, the complexity of health and safety issues is compounded by diverse work environments, varying levels of regulatory compliance, and evolving industrial practices. This blog explores common health and safety complaints, provides real-life Indian case studies, and offers practical solutions to address these issues effectively.
Table of Contents
Common Health and Safety Complaints
- Inadequate Safety Training Workers often complain about insufficient safety training, which can lead to improper handling of equipment, exposure to hazardous materials, and a general lack of awareness about workplace safety protocols.
- Unsafe Working Conditions Unsafe working conditions can include poorly maintained equipment, inadequate personal protective equipment (PPE), and unsafe physical environments. These conditions increase the risk of accidents and health issues.
- Lack of Proper Safety Equipment Employees may report the absence or inadequacy of safety equipment such as helmets, gloves, goggles, or fire extinguishers. Proper PPE is essential to protect workers from potential hazards.
- Inadequate Emergency Procedures Complaints often arise when employees are not familiar with emergency procedures or when these procedures are not clearly communicated or practiced regularly.
- Health Hazards Exposure to hazardous substances or environments, such as chemicals or extreme temperatures, can lead to health complaints. Lack of ventilation, improper waste disposal, and exposure to toxic materials are common issues.
Real-Life Indian Case Studies
Case Study 1: Fire Safety at a Textile Factory in Gujarat
In 2017, a devastating fire at a textile factory in Surat, Gujarat, highlighted critical safety lapses. The fire, which resulted in numerous casualties, was attributed to inadequate fire safety measures and the absence of proper emergency exits. Workers had complained about the lack of fire drills and emergency preparedness, which were not addressed by the management. The incident led to a comprehensive review of fire safety regulations in the textile industry and stricter enforcement of safety standards.
Citation: “Surat Fire Tragedy: What Went Wrong and What Can We Learn?” Economic Times, July 15, 2017.
Case Study 2: Chemical Exposure at a Pharmaceutical Plant in Mumbai
In 2019, workers at a pharmaceutical plant in Mumbai experienced health issues due to exposure to toxic chemicals. Despite repeated complaints about inadequate ventilation and safety measures, management failed to implement necessary changes. The situation worsened, leading to respiratory problems and other health issues among workers. The case led to a legal battle and prompted a review of safety protocols in the chemical manufacturing sector.
Citation: “Health Hazards at Mumbai Pharmaceutical Plant: A Case Study,” Business Standard, March 12, 2019.
Case Study 3: Construction Site Safety in Delhi
A 2020 incident at a construction site in Delhi involved a serious accident due to the collapse of scaffolding. Workers had previously reported concerns about the stability of the scaffolding and the lack of safety nets. The incident resulted in injuries and fatalities, highlighting the critical need for proper safety measures and adherence to construction safety regulations. This case emphasized the importance of regular safety inspections and addressing worker concerns promptly.
Citation: “Delhi Construction Site Collapse: Lessons on Safety,” Hindustan Times, June 8, 2020.
Case Study 4: Noise Pollution in an Auto Manufacturing Plant in Chennai
In 2021, employees at an auto manufacturing plant in Chennai raised complaints about excessive noise levels, which were affecting their hearing and overall well-being. The management had not adequately addressed these concerns, despite regulations mandating noise control measures. The case led to an investigation by labour authorities and subsequent improvements in noise control and employee health monitoring.
Citation: “Chennai Auto Plant Noise Pollution: Health Impact and Remedies,” The Hindu, September 22, 2021.
Case Study 5: Ergonomic Issues in a Call Center in Bangalore
A call centre in Bangalore faced complaints in 2022 related to ergonomic issues, including poor seating arrangements and prolonged computer use. Employees reported musculoskeletal disorders and eye strain. The management initially underestimated the severity of these complaints but eventually implemented ergonomic assessments and improvements, highlighting the importance of addressing ergonomic risks in office environments.
Citation: “Addressing Ergonomic Challenges in Call Centers: A Bangalore Case Study,” Deccan Herald, December 5, 2022.
How to Address Health and Safety Complaints
- Conduct Regular Training Implement comprehensive safety training programs that cover proper equipment use, emergency procedures, and hazard recognition. Ensure that training is conducted regularly and updated as per industry standards.
- Maintain Equipment and Work Environment Regular maintenance of equipment and upkeep of the work environment are essential. Conduct frequent inspections and address any identified issues promptly to prevent accidents and health problems.
- Provide Adequate Safety Equipment Ensure that all employees have access to and use appropriate PPE. Regularly review and update safety equipment requirements based on the nature of the work and potential hazards.
- Establish and Communicate Emergency Procedures Develop clear emergency procedures and ensure that all employees are familiar with them. Conduct regular drills to reinforce these procedures and make improvements based on feedback.
- Monitor and Address Health Hazards Implement measures to control exposure to hazardous substances and environmental conditions. Provide health checks and ensure that safety measures align with regulations and best practices.
- Encourage and Address Complaints Create a system for employees to report safety concerns without fear of retaliation. Address complaints promptly and transparently to build trust and ensure a safe work environment.
Don’t accept injustice just because the opponent is powerful! Take charge with Kanoon 360, the quickest & easiest Consumer Forum for consumer complaints in India. Visit our website or contact us today!
FAQs
Q: What should I do if I notice a safety hazard at work?
A: Report the hazard to your supervisor or safety officer immediately. If the issue is not addressed, escalate the complaint through the appropriate channels, such as the company’s safety committee or regulatory bodies.
Q: How can I ensure that my workplace safety training is effective?
A: Regularly update training materials based on current industry standards and regulations. Include practical exercises and assessments to ensure that employees understand and can apply the training. Gather feedback to continuously improve the training program.
Q: What are my rights if my employer fails to address health and safety complaints?
A: Employees have the right to a safe work environment. If your employer fails to address legitimate health and safety complaints, you can report the issue to relevant regulatory bodies or labor authorities. Legal action may also be an option if the situation does not improve.
Q: How can small businesses afford to implement effective safety measures?
A: Small businesses can start by prioritizing the most critical safety measures and gradually implementing additional improvements as resources allow. Seek advice from industry associations or government programs that offer support for safety compliance.
Q: What role do employees play in maintaining workplace safety?
A: Employees play a crucial role by following safety protocols, reporting hazards, participating in training, and providing feedback on safety practices. Their active involvement helps create a safer work environment.
Also Read: HyugaLife: Transforming Wellness in India and Addressing Consumer Concerns
Conclusion
Addressing health and safety complaints is essential for creating a safe and productive work environment. By understanding common issues and implementing effective solutions, organizations can prevent accidents, protect employee health, and comply with regulations. Real-life case studies from India underscore the importance of proactive measures and the impact of neglecting safety concerns. Through regular training, proper maintenance, and open communication, businesses can address safety complaints effectively and ensure a safer workplace for everyone.
References:
- Economic Times. (2017). Surat Fire Tragedy: What Went Wrong and What Can We Learn?
- Business Standard. (2019). Health Hazards at Mumbai Pharmaceutical Plant: A Case Study.
- Hindustan Times. (2020). Delhi Construction Site Collapse: Lessons on Safety.
- The Hindu. (2021). Chennai Auto Plant Noise Pollution: Health Impact and Remedies.
- Deccan Herald. (2022). Addressing Ergonomic Challenges in Call Centers: A Bangalore Case Study.